Project Analysis No. 4
Market Sector : Carbide Round Tool Supplier in New England
Type of Machine : Walter Helitronic Vision
Problem : Due to demand, an increase in throughput is required.
Form of Contact : Phone call from distributor
Solution : Replace OEM coolant nozzles with Cool-Grind Grind-Loc System using the new Quick Release Mounting System.
The customer manufactures round carbide tools, (e.g., end mills) using a Walter Vision CNC grinding machine. The fluting setup is done on the left spindle, and gashing & OD on the right spindle. Cool-Grind reviewed the current nozzle setup that consisted of the 1/2” Loc-Line system (Fig. 1), which originally came with the machine. The operator said it was prone to moving out of position when individual coolant zones are used throughout the cycle, encouraging additional zones to be enabled just to reduce the pressure. It was deemed by the Cool-Grind engineer that the best product from the Cool-Grind catalog would be the 1/2” Grind-Loc system. This product has the flexibility of Loc-Line but has more frugal, higher pressure, coherent jets and stays in position up to 100 psi, which would represent a single nozzle on a single coolant zone as a worst case scenario.
When attaching the Grind-Loc to the solenoid valves on the machine it was decided to use the new Quick Release System. This was decided because the customer sometimes needs to reconfigure the coolant nozzles, and also removing or plugging unused Loc-Line nozzles would be out of the question during a setup. The typical approach for cooling is to aim multiple jets into the process, which then creates interference and subsequent dissipation of the jets before they can be effective. Minimizing the amount of jets is key to higher pressure and causes a more effective and precise application of the coolant. The Q. R. System is similar to an air hose coupling but without the restrictive valve, and fitted with an anti-rotation location key to ensure that a nozzle has the correct aim when put back onto the machine as it had when it was taken off previously. The Q. R. System also allows coolant ports to be plugged within seconds eliminating redundant nozzles, hence raising pressure. Although carbide grinding is usually done at a relatively low wheelspeed (20 m/s or 4,000 sfpm) the benefit of a little more pressure (80-100psi) is that the structure of the wheel can be kept cleaner without using a high pressure cleaning nozzle (high pump maintenance and incorrect use can promote tip radius breakdown). The Q. R. System also allows the use of two nozzles from a single coolant port, which is extremely convenient if following a coolant delivery strategy of one coolant zone per wheel to achieve higher pressure. In essence a Walter with three coolant zones on each side of the motor can supply 3 wheels on each side. One zone for fluting, one zone for gashing, etc. The secondary benefit of using individual zones is a significant reduction in flowrate when using a central system and adding more machines to an existing filtration system is a huge financial benefit.
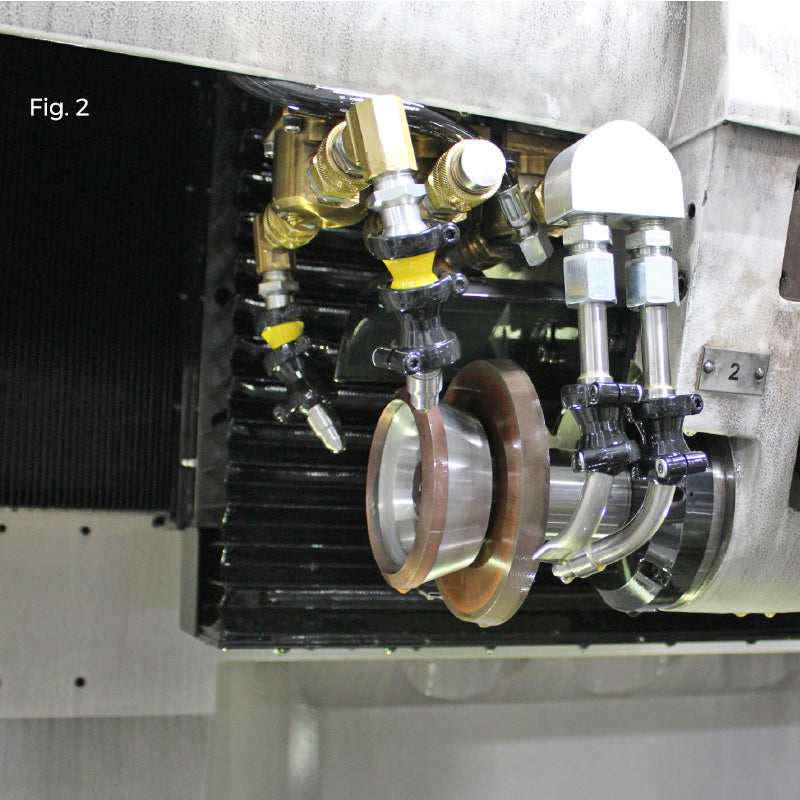